WHY IS CORROSION TESTING IMPORTANT?
Industries that use metal alloys in mild or aggressive environments rely on their metal’s corrosion performance. Generally, materials specifications for some applications include chemical composition as well as physical and mechanical properties. The corresponding corrosion resistance requirements is sometimes lacking or incomplete.
Nearly all metal alloys experience uniform or localized corrosion attack, which can be severe in aggressive chloride or other halide ion atmospheres, or in ambients containing carbon dioxide, hydrogen sulfide, water, and dissolved oxygen. The attack can start from exposure to moisture or from pre-existing residual hydrogen in the metal alloy.
Testing the conditions to which your alloys are to be exposed will lead to selecting a proper alloy. Factors impacting metal corrosion are type of alloy, treatment history, metallurgical composition, pH, composition of corroding environment, temperature, and state of internal residual stress or externally applied stress.
The attached graphical electrochemical corrosion data was generated using a hydrogen permeation electrochemical cell holding an iron (Fe) sample separating two compartments. The graph shows current decays due to oxidation reactions and current rises caused by reduction reactions. Each of the vertical fine lines highlighted in the graph depicts the start of a reaction taking place at the surface of the iron plate exposed to 0.1M H2SO4 or at its opposite surface exposed to 0.1N NaOH. Hydrogen (H) is generated in the acidic compartment by galvanic corrosion or by free corrosion of the iron surface. In the opposite surface, an oxidizing anodic potential is applied to measure the H flux permeating through the iron plate due to its galvanic coupling to zinc (Zn) or due to its free corrosion.
Assessing the metal’s corrosion response to its environment is essential and beneficial to many industries relying on metals including manufacturing, chemical, electrochemical, petrochemical, oil, refinery, construction, transportation, automotive, aerospace, energy, water cooling systems, utility, mining, electronics, food, health, and medical industry. At Corrosion Testing & Solutions, LLC (CT&S), we will assess your materials in environments relevant to your production process.
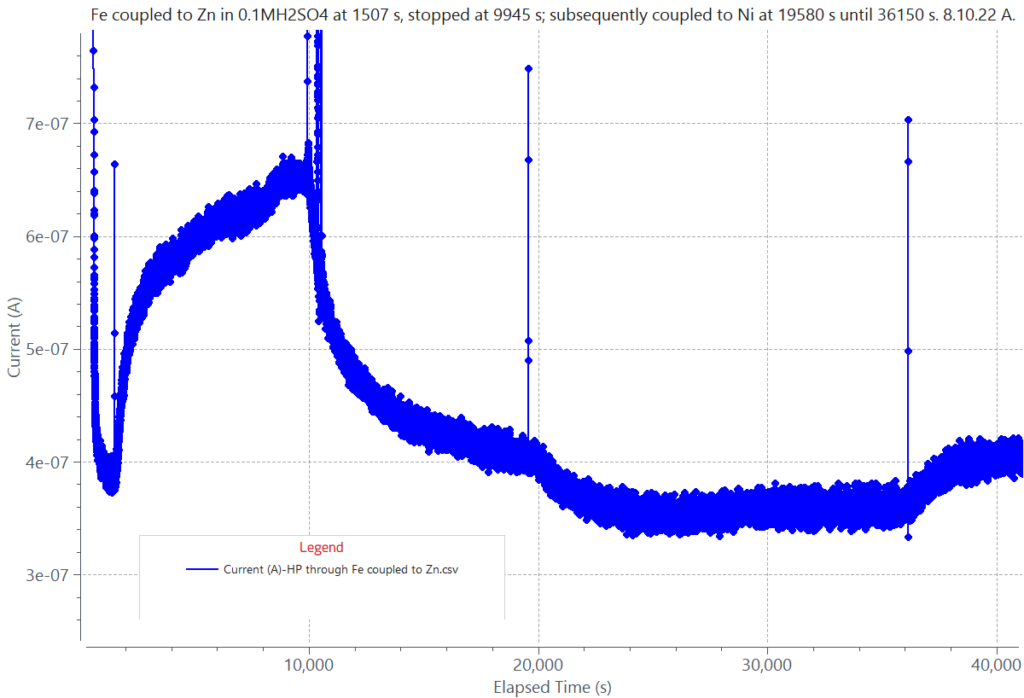