WHAT WE DO at CT&S
At Corrosion Testing & Solutions, LLC (CT&S), we provide materials corrosion consulting, corrosion testing, and corrosion training for a wide range of industries. We test your materials in environments simulating your process conditions. Testing is done according to your needs and using accepted international standards, including ASTM. We also do customized corrosion testing according to your requirements. We can help you address issues related to material failures due to uniform corrosion, crevice corrosion, pitting corrosion, inter-granular corrosion, stress corrosion cracking, hydrogen embrittlement, hydrogen entry and diffusion through metals, galvanic corrosion, or free corrosion. Examples of typical brittle fractures induced by hydrogen embrittlement are shown in the adjacent figures.
The training we provide will prepare your team on the basics of corrosion and the related science and engineering. Your team will learn about the known metal corrosion types and their respective testing procedures. You will learn to test the corrosion impact of process and materials changes relevant to your working environment. We are prepared to install a state of the art corrosion testing equipment at your facility for you to test materials or process conditions essential to your business.
Industrial metal alloys exposed to corroding mediums in processing plants require continuous monitoring. Signs of metal corrosion damage need a close evaluation to avoid failures. We can arrange a visit to your plant for a close study of the observed issues on site. Further evaluations can be done in our corrosion testing facility. We will provide you with an assessment report after completing our visit and the respective lab evaluation.

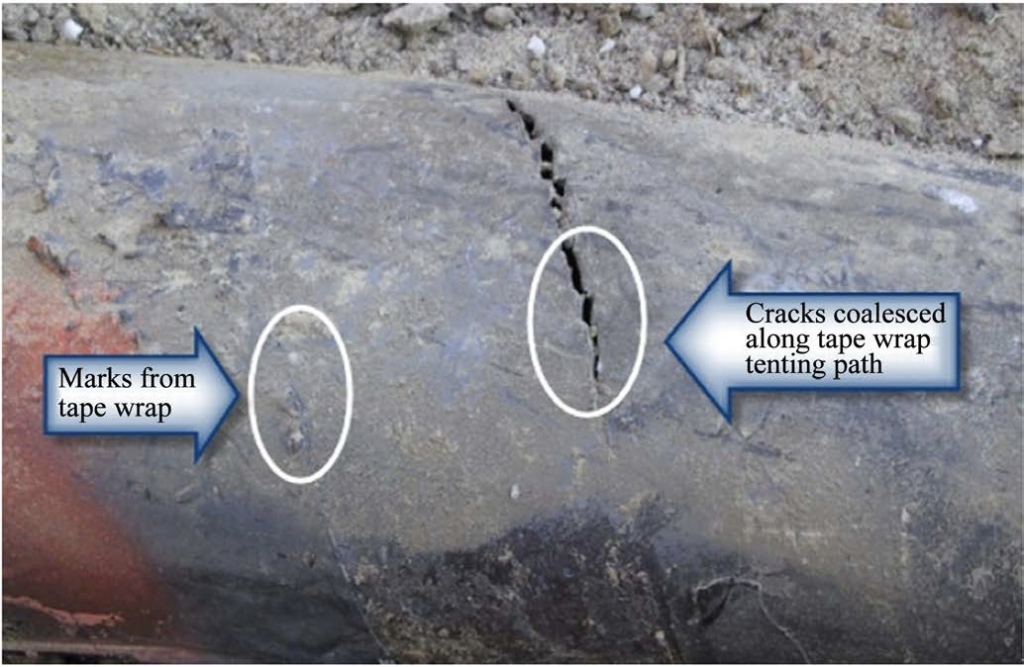