UNIFORM CORROSION
UNIFORM CORROSION
Uniform metal corrosion, called also general corrosion, takes place when the electrochemical corrosion reactions on the corroding surface occur uniformly throughout the metal surface, causing a constant weight loss rate. To quantify uniform corrosion, specimens are immersed in the corrosive environment and their weight loss is measured over a specified period. Testing is done following a standard practice for immersion corrosion test of metals according to ASTM G31 or ASTM G44. Uniform corrosion rate can also be determined by a Tafel linear polarization potential sweep covering cathodic and anodic potentials within 200 mV from the metal’s corrosion potential in the respective corroding environment. It can also be determined by an electrochemical linear polarization resistance method done polarizing the metal specimen at potentials between -20 mV and +20 mV relative to its corrosion potential.
Uniform corrosion rate can be enhanced in the presence of aggressive ingredients such as chloride ions, or other halide ions. The corrosion polarization curves in the graph below were generated with 304 stainless steel in distilled water solutions having each a different chloride content. The corrosion rates determined by Tafel analysis indicate increasing rates with increasing chloride content. Another adjacent graph displays an example of the Tafel analysis and respective corrosion parameters for 303 stainless steel exposed to a distilled water solution saturated with sodium chloride, NaCl (chloride content greater than 2.12%).
The Tafel polarization and the linear polarization resistance techniques are accurate and rapid corrosion tests, relative to the immersion corrosion test, and can be used to rank alloys and inhibitors in order of resistance to uniform corrosion. The linear polarization resistance test is done according to the potentiodynamic polarization resistance method described in ASTM G59. Potentiodynamic anodic polarization measurements are done according to ASTM G5.
Uniform corrosion of some alloys can lead to catastrophic failures. A typical example is the collapsing of the Fern Hollow bridge, Pittsburg, in 2022. The Failure was ascribed to corrosion of the metal bridge structure, a weathering steel type, poorly maintained and allowed to be exposed to water collected near the base of the bridge, which inhibited the metal from forming a protective oxide layer against corrosion. Unprotected, the metal near the base of the bridge experienced progressive corrosion and metal thinning, weakening the structure over time until the bridge collapsed; as displayed in the two attached pictures below.
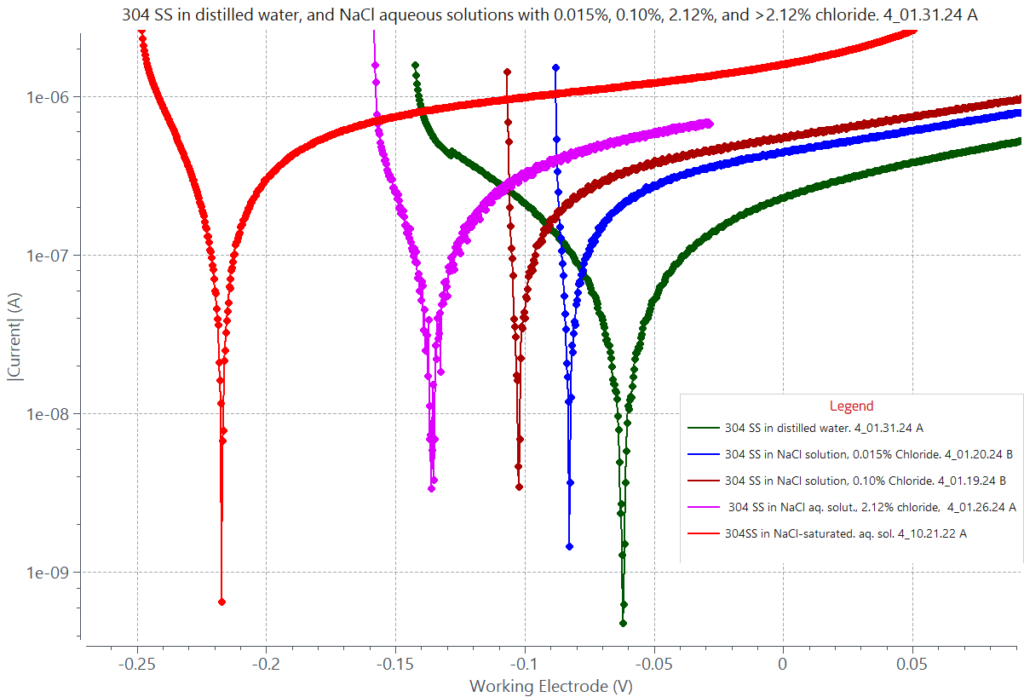
Uniform corrosion of 1cm2 area of 304 stainless steel in distilled water (green) and in sodium chloride NaCl aqueous solutions with 0.015% chloride (blue), 0.10% chloride (maroon), 2.12% chloride (pink), and > 2.12% chloride (red, saturated chloride content). 2.12% is the content of chloride in seawater (3.5% NaCl). In each case, the respective calculated corrosion rates were 0.082 µm/y, 0.113 µm/year, 0.144 µm/year, 0.313 µm/year, and 0.722 µm/year. The data shows increased corrosion rate with increasing chloride content; determined from Tafel analysis of each polarization curve near the corrosion potential.

DC Potential Tafel Linear Sweep of 1 cm2 area of 303 stainless steel (SS) in NaCl-saturated aqueous solution (> 2.12% chloride content). The Tafel analysis of the cathodic and anodic region in the log Current vs Electrode Voltage graph gave a uniform corrosion rate of 1.44 µm/year, value greater than that corresponding to 304 SS shown above. The analysis also gave a corrosion current of 124 nA, a polarization resistance of 80.3 kΩ, and a corrosion potential of -289 mV relative to a Ag/AgCl reference electrode.
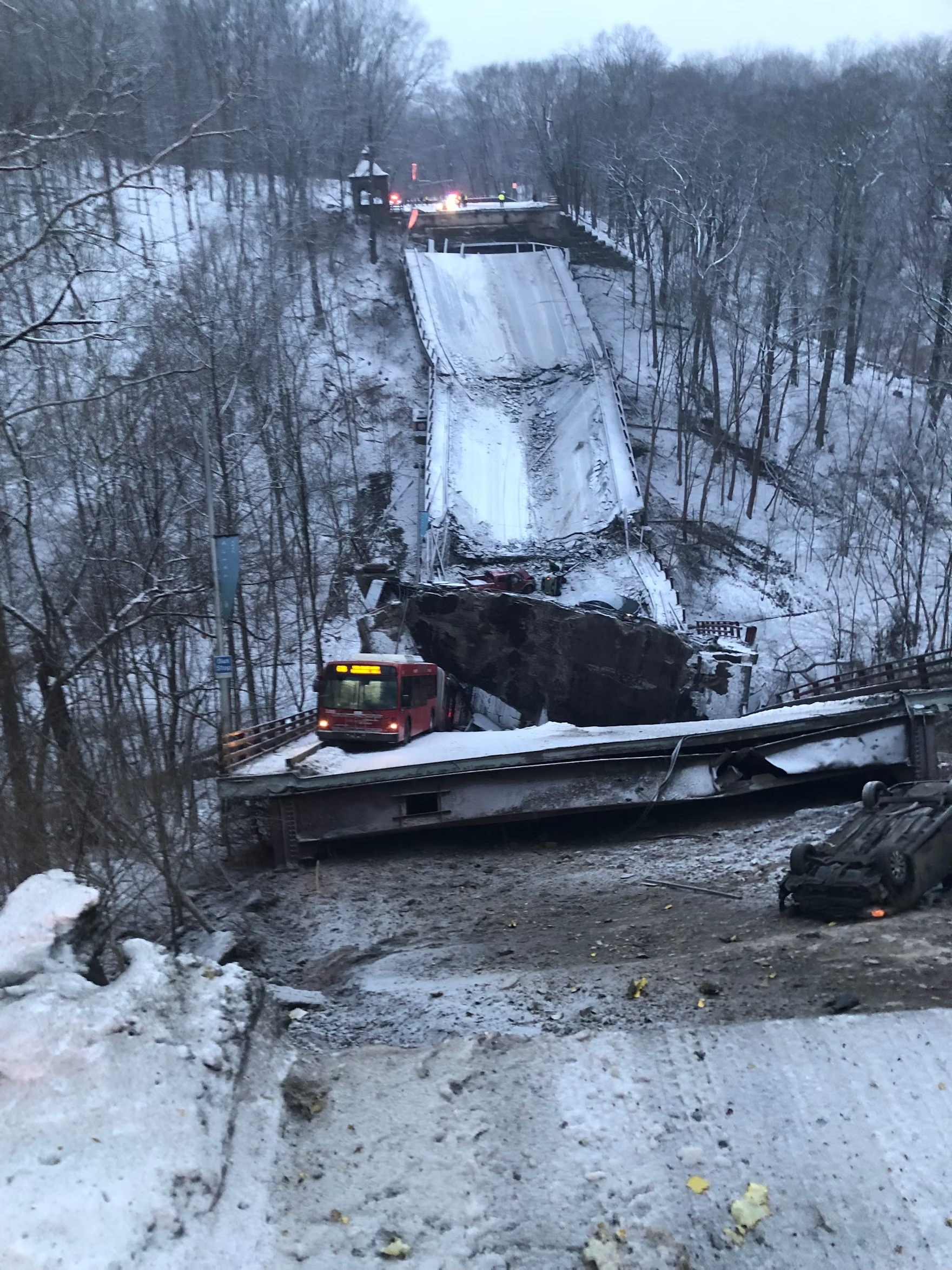
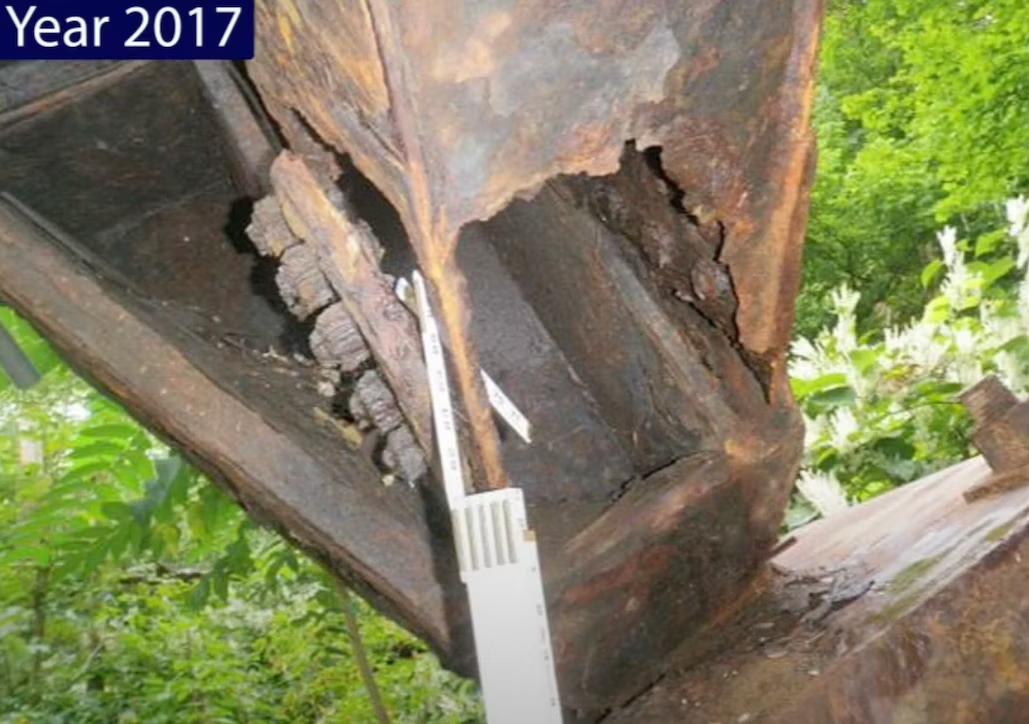