STRESS CORROSION CRACKING
UNIFORM CORROSION
Stress Corrosion Cracking (SCC) is the sudden and premature brittle failure of ductile alloys due to the combined action of tensile stress, a corrosive environment containing chloride or sulfide, and temperatures near or above 50 ºC. Cases of SCC failures near room temperature are also known to happen. The required tensile stresses may be above or be a fraction of the yield stress of the material in the form of directly applied loading stresses or as residual stresses introduced during fabrication, cold deformation, forming, welding, heat treatment, machining, or grinding.
Materials susceptible to SCC are austenitic and duplex stainless steels in concentrated chloride solutions; duplex alloys, carbon steel, and Cr-Mo low-alloy steels in solutions with hydrogen sulfide; pipeline steels in solutions of carbonate or bicarbonate containing chloride and sulfide; cupronickel alloys in seawater containing sulfur anion or ammonium cation; as well as sensitized stainless steels with precipitated carbides at grain boundaries exposed to chloride solutions. Hydrogen embrittlement (HE) is a main model considered to lead to SCC. For high strength steels, HE is the predominant SCC mechanism. The source of H arises from cathodic corrosion reactions at the metal surface which lead to atomic hydrogen absorption and diffusion into the corroding metal where it builds up to induce HE.
To minimize hydrogen-assisted cracking, reducing exposure to sources of hydrogen and reducing residual stresses is necessary. In some cases, the initiation of cracking is highly dependent on the presence of moisture. A typical example is cracking in the weld zone of transmission pipelines, as displayed in the attached graph which shows a crack along the surface path of a tape wrap where moisture likely collected to induce corrosion and hydrogen generation followed by absorption into the metal lattice.
Stress corrosion cracking resistance can be evaluated according to ASTM G103 with a bent-beam configuration test specimen according to ASTM G39 or a U-bent test specimen according to ASTM G30. Stress corrosion testing can also be done according to ASTM G44 for unstressed specimens; or according to ASTM G38 for stressed specimens. The susceptibility to inter-granular corrosion of some aluminum alloys is determined according to ASTM G67, a nitric acid mass loss test.
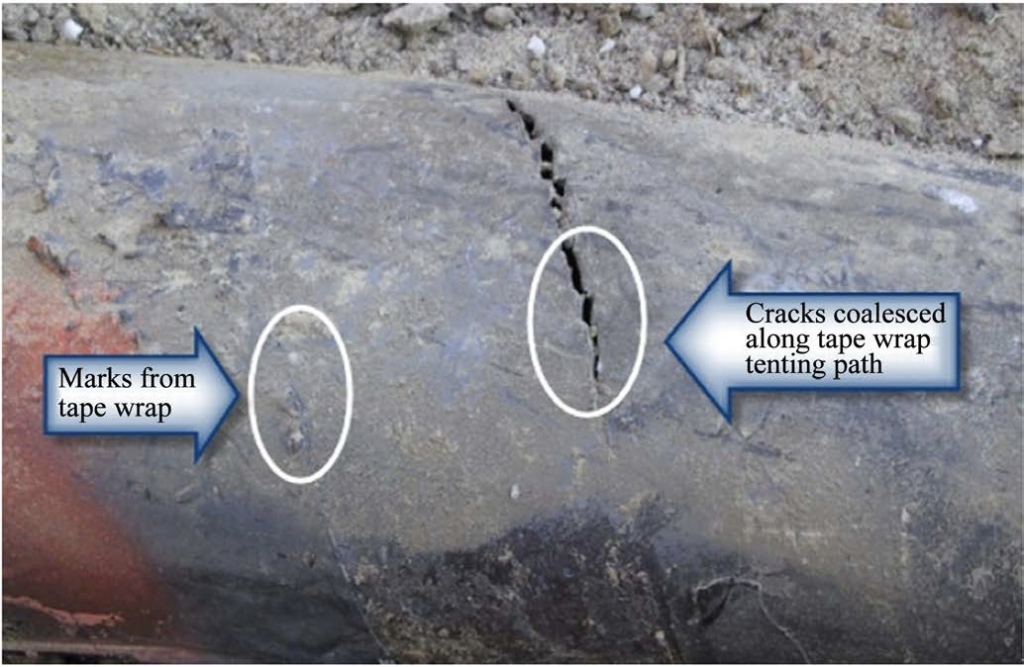