RESOURCES at Corrosion Testing & Solutions, LLC (CT&S)
At CT&S, we use our experience in corrosion science, materials science, electrochemistry, and metallurgical engineering to offer materials and corrosion consultation for a wide range of industries and corrosion environments. We perform corrosion testing using state of the art electrochemical equipment to assess corrosion rate, mode of corrosion attack, and the mechanisms leading to corrosion failure. We have a team that provides corrosion training and corrosion equipment for your business at an affordable cost for you to make corrosion measurements at your own facility. Proprietary information is well guarded and we can offer guidance for intellectual property protection.
CORROSION TESTING
We evaluate the corrosion characteristics of ferrous and non-ferrous metal alloys addressing the anodic and the cathodic reactions that take place at the corroding surface. The anodic reaction causes metal dissolution and weight loss in alloys that form a porous oxide film, or localized attack in alloys capable of forming a thin protective oxide film barrier against corrosion attack. The protective oxide film works as a barrier against ion diffusion between the alloy and the corroding environment. The cathodic corrosion reactions involve primarily reduction of dissolved oxygen, metal oxide, and/or hydrogen evolution. Hydrogen formation and absorption into the alloy from cathodic reactions is detrimental under residual or applied stress in the presence of chloride, carbon dioxide, or hydrogen sulfide at temperatures below or above 50 ºC.
Copper and copper alloys corrode by metal dissolution when exposed to an aggressive marine ambient. The graph below shows the corrosion characteristics of copper when it is polarized at room temperature in a 3.5% sodium chloride solution, which represents the chloride content in seawater. The graph shows, respectively, a cathodic and an anodic linear potential region below and above the copper corrosion potential at -0.228 V (Ecorr). The anodic dissolution region above Ecorr shows a steep linear current rise, called linear anodic Tafel region, indicating uninhibited copper corrosion by metal dissolution.
Examples of alloys that resist to metal dissolution during corrosion are stainless steels. The adjacent graph displays a maroon curve, corresponding to the polarization behavior of copper, and a blue curve corresponding to the polarization behavior of 303 stainless steel (SS) in 3.5% NaCl solution at room temperature. Unlike copper, the anodic Tafel dissolution region of 303 SS from -0.125 V to about +0.027V, above its Ecorr at -0.166 V, exhibits a significantly suppressed current. This region is followed by a passivation region of suppressed current due to the formation of a protective oxide film, which suppresses metal dissolution. The protective oxide film in stainless steel is primarily chromium oxide, Cr2O3. Each of the current spikes seen starting at 0.061 V is due to a breakdown of the oxide barrier by the action of chloride followed by its immediate re-passivation. Oxide breakdown and re-passivation events take place in the passivation region until reaching the steel pitting potential at about 0.265 V. Beyond the pitting potential the alloy is unable to re-passivate, resulting in a fast current rise due to fast alloy dissolution at the formed pits whose density increases, as shown in the figure below.
Note the contrast in the anodic curve of copper (maroon) and that of 303 SS (blue) in the adjacent graph. The current rise during the anodic dissolution of copper in the linear Tafel region is a few orders of magnitude greater than that of 303 SS because of the lack of a protective passivating oxide film on copper.
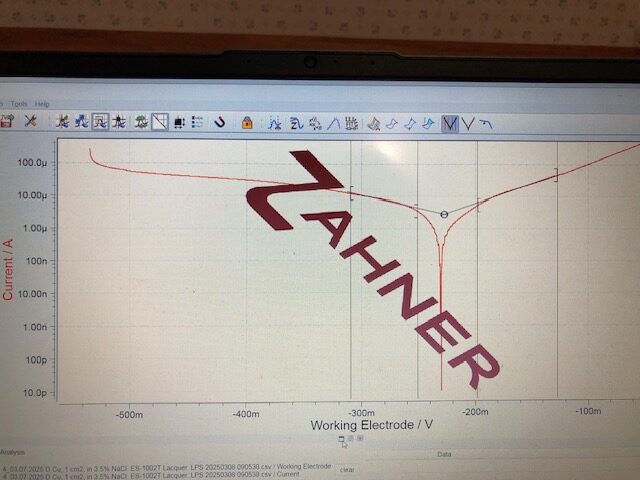
Polarization linear sweep of copper, 1 cm2, in 3.5% NaCl solution at room temperature. The graph shows a linear Tafel cathodic region below the copper corrosion potential at -0.228 V vs. Ag/AgCl. Above the corrosion potential, a steep and linear Tafel anodic region is seen. The steep slope in this region indicates large anodic currents due to substantial metal dissolution taking place during polarization in this region. The calculated corrosion rate of copper from the linear cathodic and anodic Tafel regions was 26.7 µm/y, more than ten times greater the corrosion rate of 303 stainless steel in 3.5% NaCl solution.
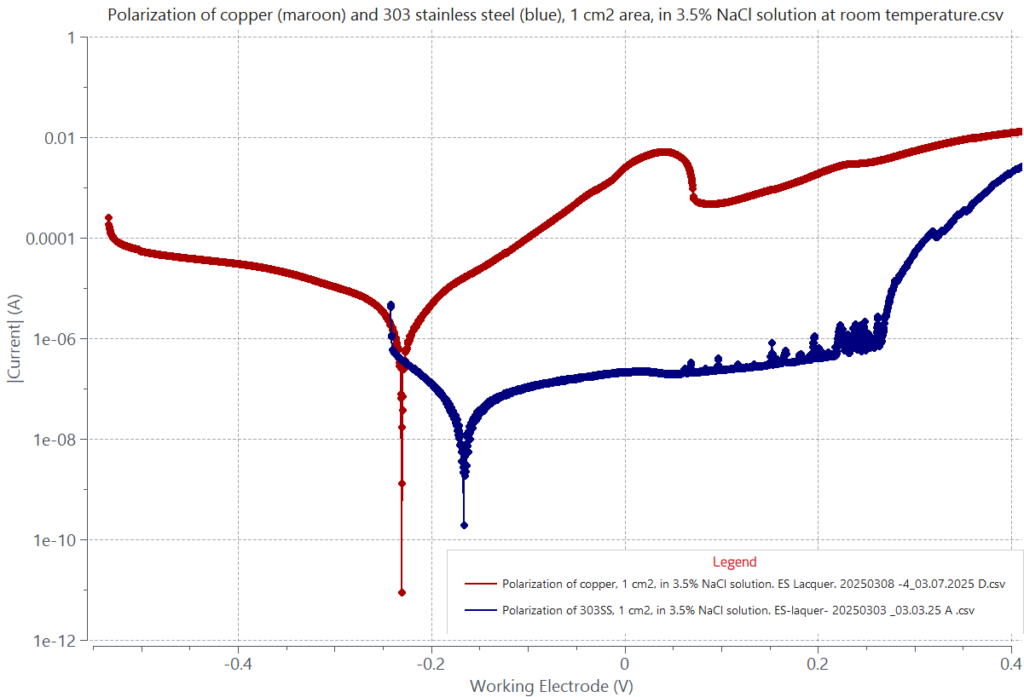
Polarization behavior of 303 stainless steel, 1 cm2, in 3.5% NaCl solution at room temperature (blue curve). It contrasts that of copper (maroon curve) whose anodic linear region is steep. The anodic Tafel region of 303 SS above its corrosion potential at -0.166V is a linear dissolution region up to 0.027V, followed by a passivation region up to 0.265V. Both regions show a shallow slope with suppressed current and metal dissolution. Beyond the pitting potential at 0.265V, a large increase in current is seen due to a breakdown of the oxide barrier passivating film caused by the chloride content in the solution.
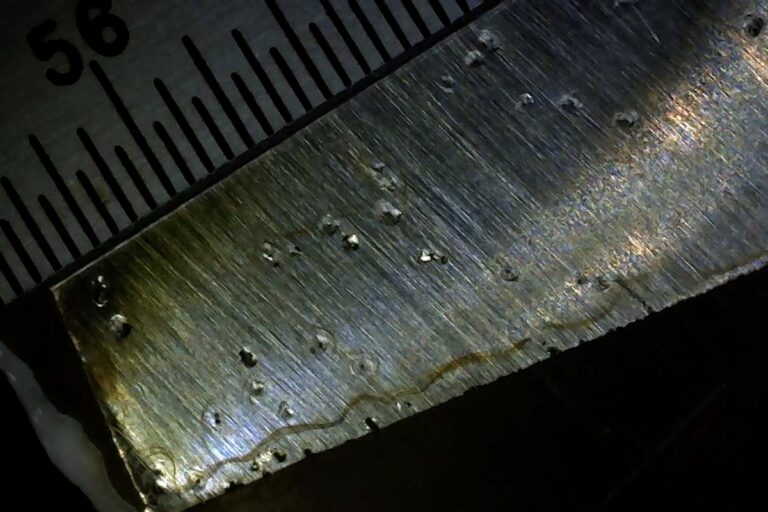
Pits formed on 303 stainless steel after polarizing this alloy in 3.5% NaCl solution to potentials beyond its pitting potential (0.263 V vs. Ag/AgCl).
METALLURGICAL CHARACTERIZATION
Metal free corrosion, galvanic corrosion, electrolytic surface pre-treatments, or cathodic protection practices can result in unwanted hydrogen charging into a metal. Heavy introduction of hydrogen into a metal, such as during cathodic protection by electrolytic means, will lead to dislocation generation and lattice metal deformation. The figure below shows iron deformation after hydrogen cathodic charging in 5% sulfuric acid. The deformation formed surface slip lines in the absence of applied stress. Slip lines are steps on the metal surface formed by the sliding of blocks of crystals over one another along slip planes.
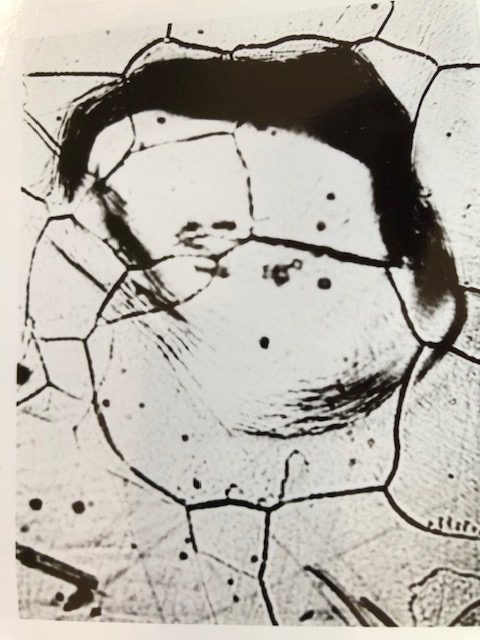
Back surface of Fe plate, 500 µm thick, cathodically charged from its opposite front surface at 25 mA/cm2 in 5% H2SO4 for 5 hours. Hydrogen loading by the cathodic charging caused lattice deformation and surface slip lines due to the deformation. No stress was externally applied during the hydrogen cathodic charging. 200X.
CORROSION INHIBITION
Different types of corrosion inhibitors can be used to suppress metal surface corrosion. Inhibitors form a thin protective film against corrosion and are selected depending on the kind of alloy and the type of corroding environment. At CT&S we can determine the inhibition efficiency of inhibitors selected for a given metal alloy and process environment.
Corrosion inhibition can also be achieved by Cathodic Protection, a cathodic polarization technique practiced to protect steel structures buried in soil, embedded in concrete, or exposed to marine and other aggressive environments. In Cathodic Protection, the metal structure is polarized cathodically using a sacrificial anode or by impressing a current with a direct current (DC )source.
New passivation methods have been developed in recent years using nano particle coating. Metal passivation using microporous oxide nanoparticle suspensions has shown to provide largely improved corrosion resistance to metals including stainless steel (SS), carbon steel, and aluminum. The metal oxide porous thin film is prepared from nano particulate dioxides of metals such as titanium, silicon, or zirconium. The attached figure shows two stainless steel plates after exposure to moist air. The non-corroded bottom-half surfaces were coated with a film of nano particles, and the corroded top-half surfaces were uncoated. A metal surface coated with such nanoparticle coating can have a largely increased pitting potential, which translates in a substantial enhancement in pitting resistance. The green curve in the adjacent figure demonstrates pitting corrosion inhibition by an increase of more than 0.5V in pitting potential for 316 SS coated with a nano particle oxide of zirconium exposed to a marine solution, relative to uncoated 316 SS (black curve). If you are interested in the microporous oxide application, contact us at
608-345-6678, MOST website
For further information on your corrosion management needs, please contact us at the links below.
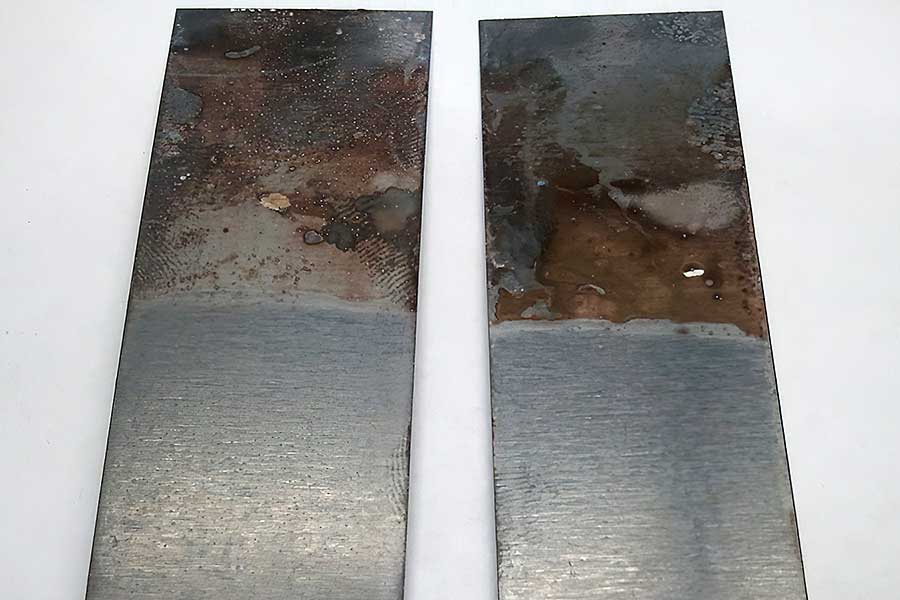
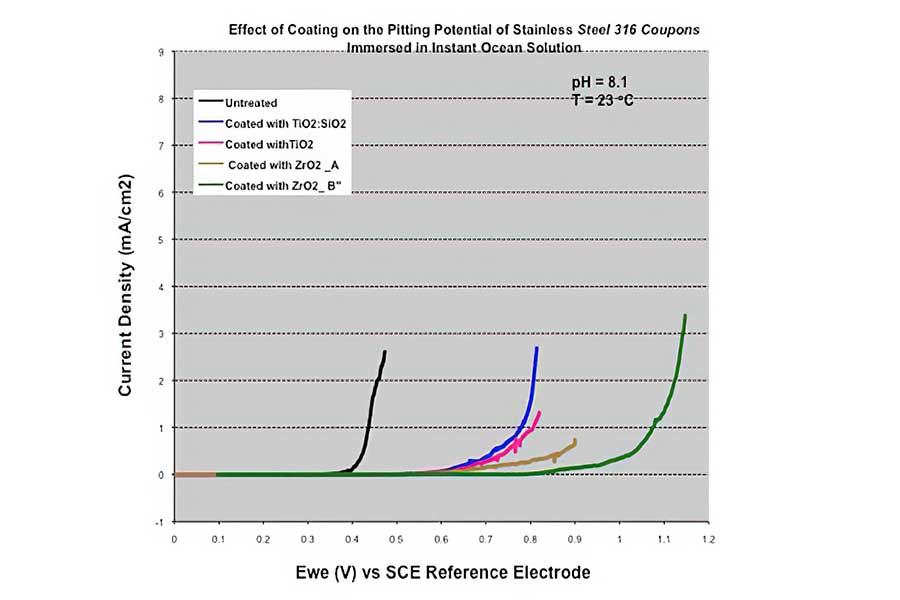
316 Stainless steel plates, after exposure to moist air, whose bottom half surfaces were coated with nano particle materials showing no corrosion. The top non-coated half surfaces exhibit substantial corrosion.
Pitting potential is the voltage at which a sharp and continuous rise in anodic current occurs during anodic polarization, as shown in the graph. In ocean solution such potential for uncoated 316 stainless steel is at about 0.4 V (black curve) and for microporous zirconium oxide-coated sample is at about 0.95 V (green curve). The pitting potential of the coated 316 SS increased by more than 05 V, substantially enhancing its resistance to pitting attack.