GALVANIC CORROSION
UNIFORM CORROSION
Galvanic corrosion takes place when two dissimilar alloys are electrically connected and simultaneously exposed to the same corroding environment. Once coupled, the less corrosion resistance alloy becomes the anode which corrodes and looses weight. The alloy with the more noble corrosion potential becomes the cathode experiencing reduction reactions and it is protected against corrosion. The corrosion at the anode electrode is enhanced by the galvanic coupling and by the magnitude of the difference in the corrosion potential between the coupling metals. The attack is greatest near the junction of the dissimilar metals and becomes larger the larger the cathode surface area is.
Some steel alloys can be protected against corrosion with a metal coating film such as zinc (Zn) or cadmium (Cd). The coated alloys become susceptible to galvanic corrosion when the deposited film (Zn or Cd) is nonuniform, is deteriorated, or is damaged. A damaged protective metal film exposes the underlying steel surface to the same corroding environment as that of the metal film and sets up a galvanic couple with the steel substrate. The current generated by the galvanic coupling will drive the corrosion of the protective film until it is consumed, leaving the steel substrate unprotected.
To assess the severity of a corrosion attack induced by coupling two dissimilar alloys, their respective corrosion potential and the galvanic corrosion current generated by the coupling can be measured. If your process requires dissimilar alloys to be in contact while simultaneously being exposed to the same corroding environment, we can help assess the respective corrosion risk applied to your process environment.
The magnitude of the galvanic current from coupling two dissimilar alloys depends on the difference between their respective corrosion potentials in the corroding solution. The attached graphs display the galvanic current generated from coupling iron to zinc and iron to aluminum in a 0.1M H2SO4 solution. The current generated by coupling iron to zinc is about 8.70 mA, and that from coupling iron to aluminum is 20 µA, for the same cathode to anode area, iron being the cathode in both cases. The relatively large galvanic current of the iron-zinc couple will cause zinc to be aggressively corroded while hydrogen evolution is expected to take place on the iron surface. In contrast, the small galvanic current of 20 µA will induce minimum corrosion on aluminum when coupled to iron. Assessment of galvanic corrosion can also be done by overlaying the polarization curves of each of the coupling alloys tested separately in the same corroding environment.
The standard method to evaluate Galvanic corrosion tests in electrolytes is ASTM G71.
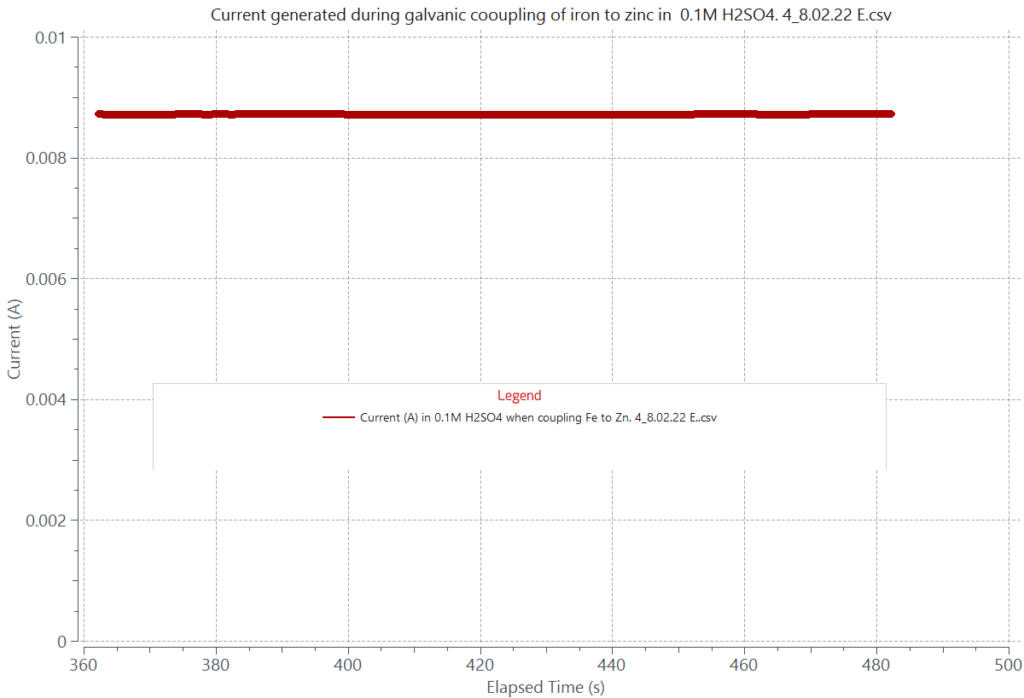
Galvanic current due to room temperature galvanic coupling of a zinc plate to a 500 µm thick iron plate, 1 cm2 area, in 0.1M H2SO4 solution. The generated current by the coupling is about 8.7 mA.
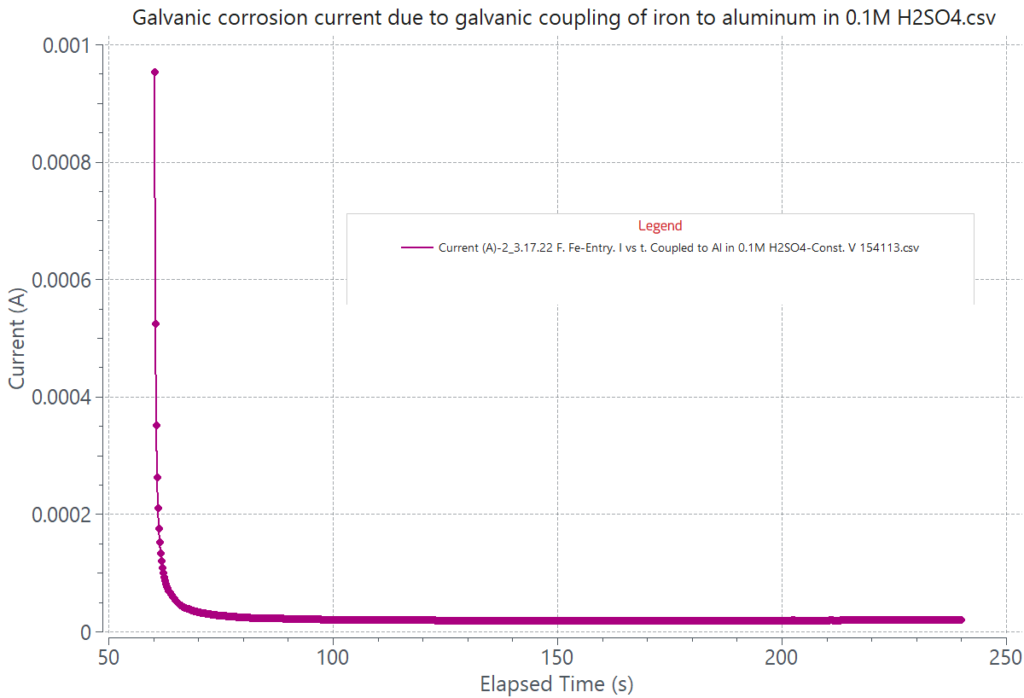